The Lasting Impact COVID-19 Has on the Global Supply Chain
Last Updated July 26, 2023
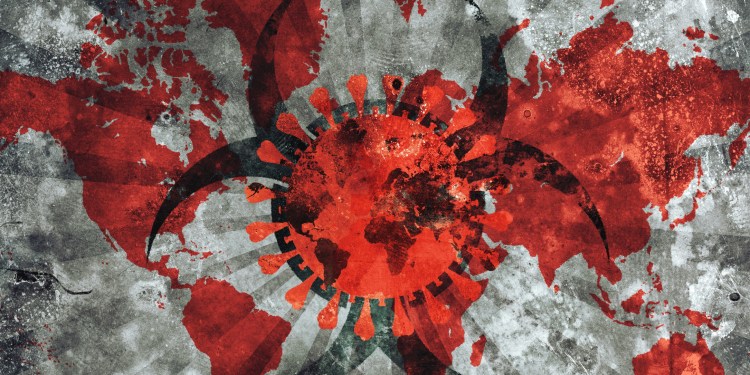
A huge part of supply chain management is being prepared for disruptions, from materials shortages to natural disasters, with a contingency plan. When the disruption is a highly communicable disease outbreak that has become a global pandemic and has brought the world’s manufacturing hub to a standstill, is your contingency plan enough?
That’s what global suppliers, manufacturers and retailers in multiple industries are faced with in the midst of the COVID-19 pandemic.
“We’re grasping for precedents,” says Phil Levy, chief economist at Flexport and economic adviser in the George W. Bush administration.
In the unprecedented shutdown of urban centers, including the world’s primary supplier and manufacturer, and now shipping and supply chain bottlenecks, when do contingency plans become the new normal? As some of the biggest companies in the world have had to deal with major disruption to their number one supplier, could this force a supply chain shift away from China, permanently? Let’s look at the impact so far and where it could lead.
What Are the Greatest Areas of Impact?
China accounts for 16% of global economic output and with $2.7 trillion in exports, it’s arguably “the manufacturing center of the world” with cities that have become manufacturing hubs, clustered around various industries.
With China’s manufacturing centers still revving back up after previous lockdown or quarantine orders to prevent the spread of the virus, supplies are backlogged after manufacturers and suppliers in entire industry sectors had to halt production throughout 2020.
According to a “Business Impact of the Coronavirus” study by data firm Dun & Bradstreet, at least 51,000 global companies have one or more direct, or Tier 1, suppliers in the impacted Chinese provinces, with at least 5 million global companies having one or more Tier 2 suppliers located there. Two of the hardest hit industries are:
Automotive Industry
Ground zero of the coronavirus outbreak was the city of Wuhan, a major automotive parts manufacturing hub and home of Dongfeng Motor, “one of the largest and most diversified joint venture automakers in China,” according to CNBC. Besides Dongfeng, French car parts maker Valeo has multiple facilities in Wuhan and Honda and General Motors have factories in Wuhan’s Hubei province—all of which shutdown during the city- and province-wide lockdowns in 2020.
While automakers, including Tesla, Ford, General Motors and Toyota, slowly re-started production at their assembly plants in other Chinese provinces, “based on supply base availability, employee health concerns and local government recommendations” according to one GM spokesman, Wuhan’s role as a global automotive components producer impacts automotive assembly plants around the world, even a year and a half after the initial outbreak and closures.
Seoul-based Hyundai had to idle all seven of its assembly plants in South Korea due to a shortage of Chinese-made components, according to an AP report. Similarly, Fiat Chrysler Automobiles saw four of their “critical components” suppliers based in China shutdown and temporarily halted production at one of their European-based plants.
It takes an average of 30,000 parts in the assembly of one vehicle, and “the bad news for the auto industry is that it only takes one component to take down the production of a vehicle,” says Mike Wall, automotive analyst at IHS Markit.
Collectively, U.S. automakers source 15% of their components from China, meaning the 2020 shuttering of Wuhan’s factories and suppliers continues to create a ripple effect. Many of the plants that initially went unscathed by parts shortages experienced shutdowns and backlogs as “automakers across the US and Europe declared temporary shutdowns to halt the spread of COVID-19,” according to CNET Road Show writer Sean Szymkowski.
High-Tech Industry
As the world’s largest manufacturer of mobile phones, computers and televisions, and the components needed to build them, China’s shutdown of its technology manufacturing centers disrupted the high-tech industry’s supply chain.
Perhaps no global tech company is more invested, or stands to lose more, in China than Apple. The company’s two Foxconn-contracted plants in Shenzhen and Zhengzhou, the latter the world’s largest iPhone factory in a 1.4 million square-meter compound dubbed “iPhone City,” were forced to shutter in the first half of 2020. Reports indicated the Foxconn plants were “struggling to return to full production” as workers must clear “epidemic control requirements” before they can report to work.
The impact of the shutdowns forced Apple to slash its sales expectations for the quarter, with the tech giant stating in a letter to investors, “we do not expect to meet the revenue guidance we provided for the quarter” as the “worldwide iPhone supply will be temporarily constrained” with manufacturing “ramping up more slowly than we had anticipated.”
“This episode is going to make it even clearer to Apple that there is overconcentration in China and they may want to address that,” says Don Yew, an analyst with investment firm Morningstar Asia.
While overall cell phone import figures for 2021 have so far been consistent with 2019’s pre-pandemic levels, an “unseasonal drop” of imports over the summer could be an indicator of residual supply chain issues and the shipping backlog, explains Jason Miller, associate professor of supply chain management at Michigan State University. “September and October are the biggest months for importing cell phones, so time will tell whether the August drop was a harbinger of problems.”
Is This the Tipping Point for China as the World Supplier?
Curtis Chin, an Asia fellow at the Milken Institute, put it simply to CNBC: “It can’t all be in China, we’ve seen some of the consequences of over reliance on just one key market.”
This key market has grown in importance and sophistication over the last two decades, from a producer of cheap, disposable goods to the world’s second-largest economy controlling 70% of the global supply of raw materials. The China that was shut down by a similar health panic in 2003 (the SAARs outbreak) is not the same China of today, just as COVID-19 has proved to be deadlier and harder to contain than SAARs.
The coronavirus-fueled shutdown of China and subsequent domino effect on global manufacturing and shipping may be the third strike for many companies, after the disruptive months-long protests in Hong Kong and the trade war between China and the United States, resulting in billions of dollars in tit-for-tat tariffs on goods from both countries.
China’s clout on the world stage, its increasingly competitive and sophisticated home-grown enterprises (think Huawei) and the obvious interdependence of U.S. companies and U.S. economy as whole on China led to the Trump administration’s justification for trade tariffs.
“The coronavirus more than the trade war has sped some of that decoupling as countries, as businesses, think about their supply chain for the long run,” says Chin. “The reality is that the U.S. and Chinese economies, from supply chains to investment and trade flows, will be intertwined for years to come. The coronavirus crisis, however, has underscored to the United States and all of China’s trading and investment partners the value of diversification away from China.”
With the supply chain havoc created in the wake of the COVID-19 pandemic, the Biden administration is moving away from looking at China as the issue and instead to looking squarely in the mirror. In February 2021, President Biden issued an “Executive Order on America’s Supply Chains,” stating “it is the policy of my Administration to strengthen the resilience of America’s supply chains.”
The executive order outlines Federal review for securing and strengthening critical supply chain areas, including those for the defense industry, public health, information technology, transportation, energy sector and food production and agriculture.
Is This a “Wake-Up Call” for How Supply Chains are Structured?
The Biden administration has seen it as such, with the executive order emphasizing how the pandemic and similar threats “can reduce critical manufacturing capacity and the availability and integrity of critical goods, products, and services.”
Many business prognosticators agree. “This is a wake-up call for companies thinking about designing a supply chain. Risk and resiliency need to be part of the design,” says Razat Gaurav, CEO of AI-powered supply chain analytics software maker LLamasoft. “Many companies have business continuity plans for earthquakes and floods (in China) but the alternative facilities were also in China.”
The impact to the companies and suppliers within the tech industry clustered in China reflects this. While there were multiple contract manufacturing partners that Apple and others could shift to as plants shutdown, “most of that capacity is located in regions that are under the same kind of restrictions,” writes Steve Banker in Forbes.
On-Shoring the Supply Chain
For many, this strengthens the case for more on-shore or near-shore operations. Former U.S. Commerce Secretary Wilbur Ross expressed his opinion that the Chinese shutdown due to coronavirus “does give business yet another thing to consider when they go through their review of their supply chain… So, I think it will help to accelerate the return of jobs to North America.”
Yet, completely on-shoring the supply chain or touting “domestic” manufacturing is not that simple, as the automotive industry demonstrates. The on-shoring can’t just be the manufacturing or assembly end, but also of suppliers, as this is where the inter-dependence causing these domino effects lie (i.e. Hyundai’s shutdown of all its domestic plants for lack of Chinese-made parts).
“All supply chains seem vulnerable because so many Chinese supply chains within supply chains within supply chains rely on each other for parts and raw materials,” writes Rosemary Coates, consultant and executive director of the Reshoring Institute for Logistics Management. “Purchasing departments declaring that they have alternate non-Chinese suppliers, may be naïve in thinking that their domestic suppliers don’t rely on parts from China and that shortages are eminent.”
Those Plan B “alternatives” become Plan C when your contingency plan now needs a contingency plan.
“The longer these things go on and the more disruption that occurs in the supply chain, you start diverting your production,” says management consultant Daron Gifford in Crain’s Detroit. “It’ll be interesting, after this is done, if it starts to alter some of our suppliers’ plans on how they structure their supply chain.”
But long-term diversion and a complete “uncoupling” from China is doubtful, particularly for the tech industry. Short term options just aren’t there when faced with the closure of a complex facility on the scale of Zhengzhou’s “iPhone City” or relocating semiconductor fabrication when a facility “costs $1 billion to open,” Gaurav points out.
“Today’s sophisticated supply chains took a decade to optimize,” writes Randy Brown in Forbes. “Finding alternatives for high-end manufacturing is not trivial, and the assumptions on finding alternatives are probably optimistic.”
How Lean is Too Lean?
This optimized efficiency is a testament to the success of lean manufacturing methodologies, but is that success now proving to be a double-edged sword?
Lean emphasizes improving cost and process efficiencies by eliminating waste in multiple areas, including overproduction and excess inventory. This has created “a world of just-in-time inventories” and “just-in-time shipments”—efficient, precise and designed to cut excess production, processing, or waiting. For many automotive and high-tech manufacturers, this “just-in-time” mindset has led to extremely thin buffer inventory. For example, Chris Cunnane, writing in Logistics Viewpoints, states that “on average, companies have anywhere between two and twelve weeks of buffer inventory on-hand for automotive parts.”
Lean manufacturing’s focus on logistical and cost efficiency has also led many companies to pare down their number or types of suppliers.
Automotive analyst Mark Boyadjis gives the example of car companies that once worked with six to ten different suppliers for all the needed components of high-tech automotive dashboards now “trying to get that number down to two or three”—a logical move from a logistical and efficiency standpoint. But it’s when these like suppliers become clustered in these regional hubs, such as the density in the various cities in China, that issues arise.
“Most purchasing managers try to have multiple suppliers for any given component, or at least one supplier with multiple plants in different parts of the world,” argues economics and business strategist Bill Conerly in Forbes.
However, in the high-tech and automotive supply chains especially, this is becoming less and less the case, as “regionalization” and “single source components for new vehicles [with] China a larger supplier,” as Razat Gaurav shared in an interview with Logistics Viewpoints. “Thus, there is exposed risk.”
The importance of regularly assessing the end-to-end supply chain for risks and being prepared to minimize those risks through supply chain agility cannot be overstated. This means greater transparency and real-time visibility into the supply chain, building and strengthening supplier networks, and thinking beyond “just-in-time” inventory fulfillment to “strategic inventory optimization.”
Answers in the Face of the Unknown
The extent of the human impact of the COVID-19 pandemic continues to unfold, with lopsided vaccine rollouts and stalled vaccination efforts. The extent of the impact to multinational businesses and the global economy is also still unfolding, as many sectors are struggling to re-open and re-staff and shipping delays, shortages and backlogs, primarily of goods coming out of China, are clogging supply chains.
What is clear is that “supply chains present the greatest economic threat to business from the COVID-19 virus,” writes Bill Conerly.
As automotive industry consultant Jochen Siebert predicts, “the epidemic will put the question of supply chain management squarely on the desks of CEOs.”
This level of impact reiterates the need for supply chain representation within the ranks of executive leadership.
“The supply chain is a strategic resource for most organizations,” says David Frayer, Assistant Dean for Outreach & Engagement in Michigan State University’s Eli Broad College of Business. “Unfortunately, the only time many executives think about the supply chain is during times of disruption or failure. We need to be more proactive, strategically-engaged, holistic and integrative in the way we think about the business, not only with regard to cost, but with regard to flexibility…We need to be the ones that are helping lead the organization away from a scale-based, one-size-fits-all approach toward a more resilient future that can handle the growing uncertainties of the global environment.”
Prepare to lead your supply chain through disruption.